Nonwovens Institute Awarded Grant to Study Mask Material Improvements
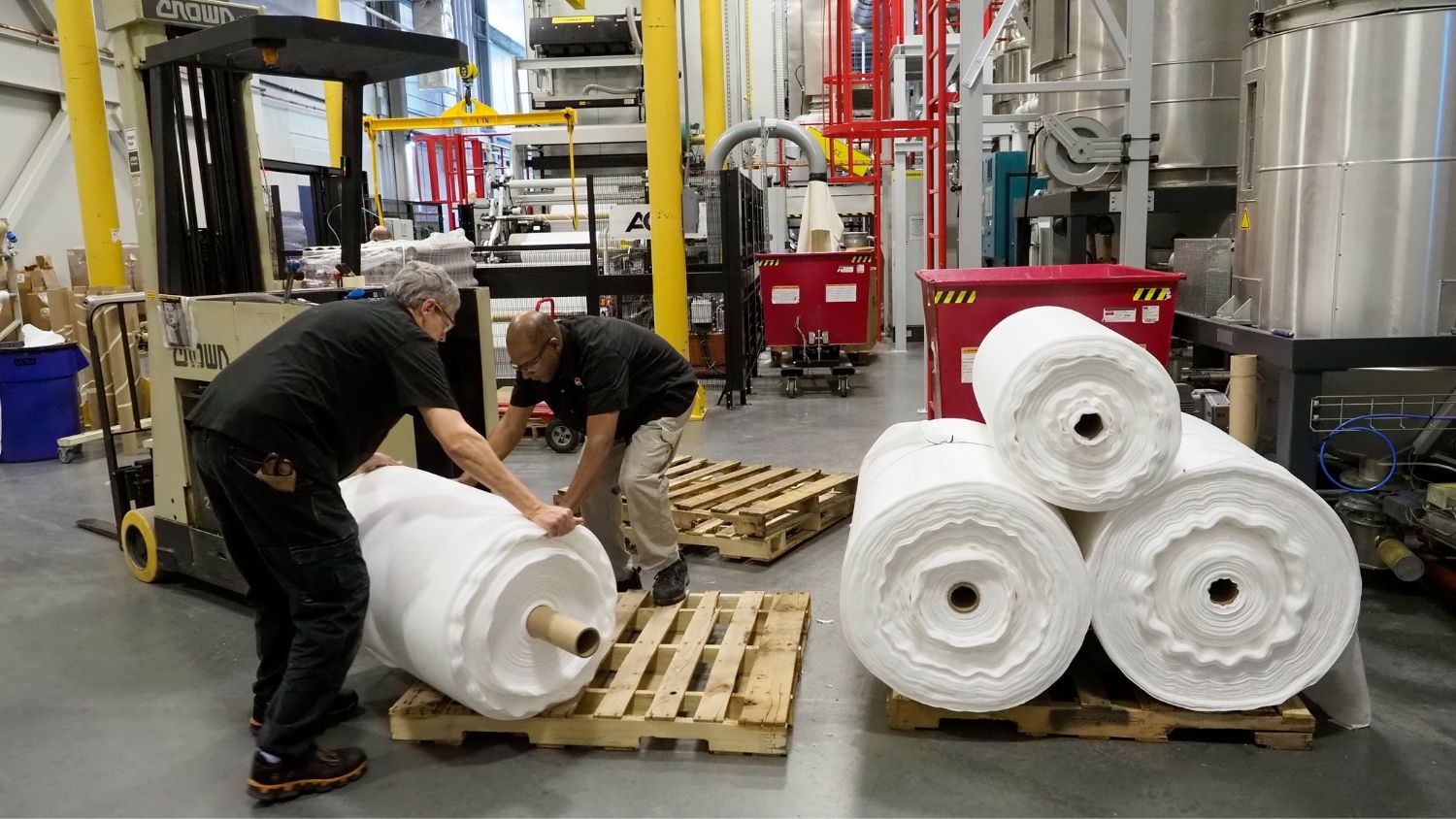
For Immediate Release
North Carolina State University’s Nonwovens Institute (NWI) received a six-month, approximately $400,000 grant from The National Institute for Innovation in Manufacturing Biopharmaceuticals (NIIMBL) to investigate improving the properties of materials they’re using for masks and respirators.
Ultimately, the researchers’ goal is to enhance the materials in order to boost performance and production capacity.
“The idea behind the grant is to improve the performance of the materials we are currently producing,” said Behnam Pourdeyhimi, executive director of NWI, Associate Dean and William A. Klopman Distinguished Professor and the project’s principle investigator.
N95 respirators and surgical masks are generally a sandwich of one or two common nonwoven layers – so-called “spunbond” layers that provide mask strength and protect the inner filtration layer – and a nonwoven meltblown material that filters microscopic unwanted particles like viruses and bacteria.
Because of the current critical need for masks caused by COVID-19, Pourdeyhimi and his NWI team created a new spunbond material that can serve as a filter without the need for a meltblown filtration layer. The unique fabric is composed of two different polymer materials that are combined to make a single fiber with significant strength and bulk, along with microfibers of a similar size to the normal meltblown filters. The new material has similar effectiveness to current filtration materials.
Since the start of the pandemic, NWI has been producing between 150,000 to 180,000 meters of this unique filter medium per week using its state-of the-art pilot facilities located at NC State’s Centennial Campus at the Center for Technology and Innovation.
To meet the demand for masks that can be worn by the general public, researchers are making single-layer masks out of the spunbond material. One of the objectives of the project funded by NIIMBL is to improve NWI’s spunbond material to meet the U.S. Food and Drug Administration (FDA) standards for surgical masks for particle filtration and fluid resistance.
“You want a mask that’s not too thick and too warm, and easy to breathe through,” Pourdeyhimi said. “What we want is a single layer that meets FDA requirements, and is not built on the meltblown filtration layer that is in short supply.”
NWI has also developed a new meltblown filtration media in its fight against COVID-19. Pourdeyhimi said his team is working around the clock five days per week to make the meltblown filtration material. NWI produces approximately 120,000 meters per week of the material.
One of the objectives of the NIIMBL grant is to improve the meltblown material that goes into three-layer surgical masks as well as into N95 respirators, which are designed to filter more than 95 percent of airborne particles at 0.3 microns.
“Part of this grant is focused on reducing the weight of the filters without adversely impacting the performance of the filter – using less fabric would increase the available capacity,” Pourdeyhimi said.
- Categories: