A Sustainable Solution
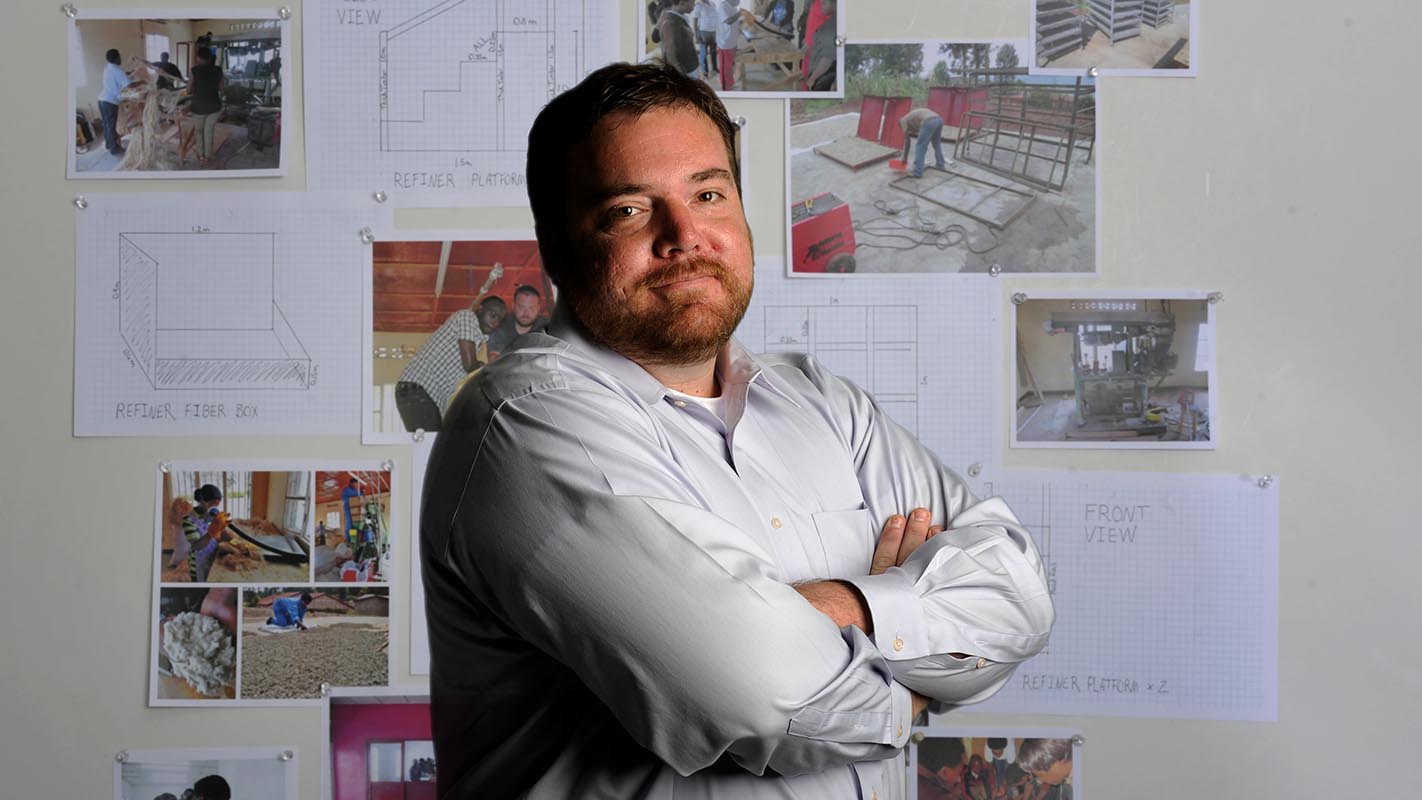
In the developing world, the absence of affordable sanitary pads is more than a health and hygiene issue — it’s an economic and educational problem, too.
The solution to that problem is a cheap, sustainable, locally sourced sanitary pad. Researchers at NC State and the Massachusetts Institute of Technology, working with nonprofit partner Sustainable Health Enterprises (SHE), developed such a solution for deployment in Rwanda.
But Raleigh and Cambridge are a long way from the Rwandan capital of Kigali. It took a particular set of skills to cover the distance between success in the lab and results in the field, skills that 32-year-old NC State junior Tyson Huffman acquired as a Marine, a construction worker, a farmer, a restaurant manager and a process engineer for a paper mill.
“He’s a prototypical example of ‘think and do.’” — Med Byrd, NC State paper scientist, on Tyson Huffman.
For most of the last year, Huffman has been in Kigali, leading the effort to build a facility that can manufacture 1,000 sanitary pads a day.
“This guy went over there and did what I don’t think any faculty member or any student could have done,” said Med Byrd, associate professor of paper science and engineering at NC State. “In the space of about three months, with no tools, he took them from two machines in the middle of a parking lot to a dedicated crew making fluff pulp.”
That pulp is the heart of the project. In 2009, SHE founder Elizabeth Sharpf and a group of MIT students set out to find a sustainable, inexpensive way to make sanitary pads from agricultural byproducts local to Rwanda. They developed a two-step process for turning banana fibers and water into a fluffy pulp and making pads from that pulp. The chemical-free material is more absorbent than anything commercially available, Byrd said.
SHE turned to NC State to take the project from the research lab to the real world. Textile and biomedical engineering professor/director of Global Health Initiatives in the Office of International Affairs Marian McCord, Byrd and others refined the process and then sought someone who could go to Rwanda in 2013 and scale the project up. Several recent chemical engineering graduates applied, but none of them had Huffman’s unique skills.
“He’s a prototypical example of ‘think and do,’” Byrd said.
Huffman has served as a “MacGyver-in-residence,” said Connie Lewin, director of marketing and strategic partnerships for SHE. When the disappearance of Huffman’s luggage on the way to Rwanda deprived the project of needed washers, he replaced them with bottle caps. He designed a process that sped fluff-drying time by 400 percent and worked with his team to build a system for recycling wastewater.
“He’s creating new tools and spending time with our staff there so when he leaves they’re fully equipped and empowered to run the production facility on their own,” Lewin said.

Eventually, SHE plans to manufacture 250,000 pads a year and distribute them cheaply to local schools, Lewin said. That could be a game-changer for Rwandan girls and women. On average, a Rwandan woman loses $215 in annual income due to work days missed during menstruation, according to SHE estimates. The average Rwandan earns $578 a year, according to the United Nations.
Success would also create economic prosperity in Kigali. Huffman manages a team of 12 Rwanda employees, and they’ll continue producing pads after he leaves. The potential for a lasting, sustainable impact drew Huffman to the SHE project.
“The word ‘sustainable’ has become a buzzword and is thrown around too loosely,” he said. “I don’t really believe in charity. Throwing money at a problem is certainly not sustainable. However, creating a business employing local people, using agricultural waste and breaking even is the definition of sustainable.”