Finding the Best Way to Get COVID-19 Test Kits Where They’re Needed
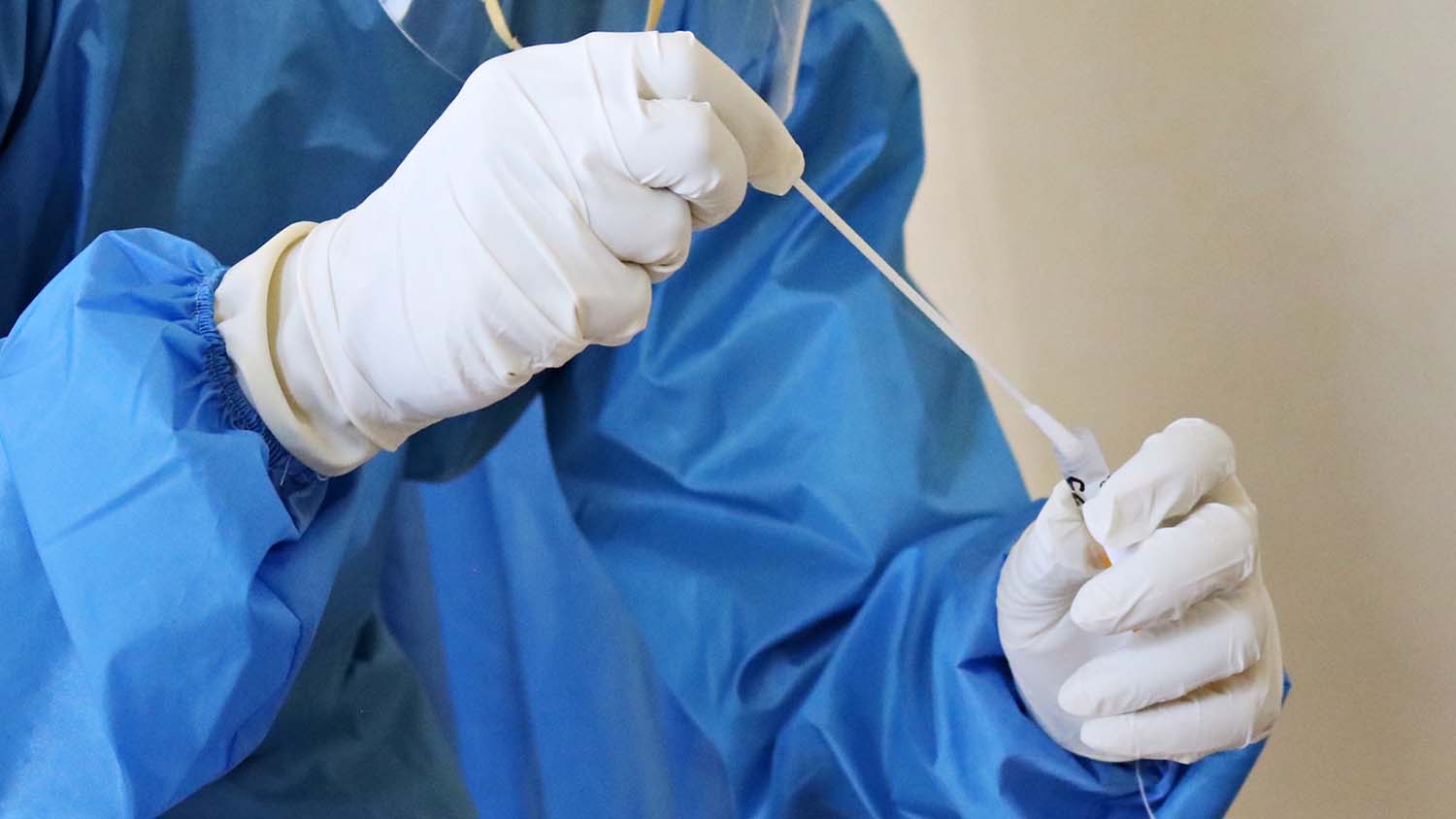
For Immediate Release
Getting accurate, timely information on COVID-19 cases is one of the major challenges facing policymakers as they make decisions about public health and the economy. Researchers at North Carolina State University are embarking on a project aimed at making sure test kits are available where they are most needed, so that policymakers have the information they need.
Specifically, researchers are developing a computational model that can be used to identify the best allocation plans for distributing test kits to hospitals, clinics, and relevant state agencies. The work is being done with support from a one-year, $600,000 grant from the National Institute for Innovation in Manufacturing Biopharmaceuticals (NIIMBL).
The model can be updated as new information becomes available, and will be used to address key questions related to COVID-19 testing:
- What is the optimal distribution of reagents and test kits for allocation to selected locations?
- What test kits should be stockpiled for use in case of a second wave of COVID-19 infections?
- How should inventory and testing capacity be positioned in order to enable both the rapid distribution of test kits and the collection, transportation, and analysis of test samples?
- How will the system adapt to changes in patient management and testing protocols as demand for kits shifts based on patterns of new COVID cases?
- What are the different strategies needed for the different types of test kits (molecular, antigen and antibody)?
“This is an extremely complex supply chain, with many different players and a host of variables to consider,” says Rob Handfield, principal investigator on the grant and Bank of America University Distinguished Professor of Operations and Supply Chain Management in NC State’s Poole College of Management. “We are going to start by developing the model for North Carolina, and will extend this to the US by the end of the project. Part of the challenge will be simply identifying all of the suppliers of test kits and materials.”
“Another challenging aspect is that a ‘kit’ can mean different things, from just the materials that are needed to collect the biological sample and preserve it, to the personal protective equipment required to protect the health care worker collecting the sample,” says Don Warsing, a co-investigator on the grant and associate professor of operations and supply chain management at NC State.
“This space is moving and changing very rapidly, and the nature of the crisis is such that outbreaks continue to pop up and shift over time. One challenge we’re working on is a way to dynamically, and fairly, allocate limited supplies to the points of greatest need.”
The team hopes to develop a working prototype of the model and implementation protocols for North Carolina by later this year, and a working national model by June 2021.
NIIMBL is a public-private partnership whose mission is to accelerate biopharmaceutical innovation, support the development of standards that enable more efficient and rapid manufacturing capabilities, and educate and train a world-leading biopharmaceutical manufacturing workforce, fundamentally advancing U.S. competitiveness in this industry. NIIMBL is funded through a cooperative agreement with the National Institute of Standards and Technology in the U.S. Department of Commerce with significant additional support from its members.
This work was performed under financial assistance award 70NANB20H037 from the U. S. Department of Commerce, National Institute of Standards and Technology.
-shipman-