Researchers Create Shape-Shifting ‘Transformer Bots’
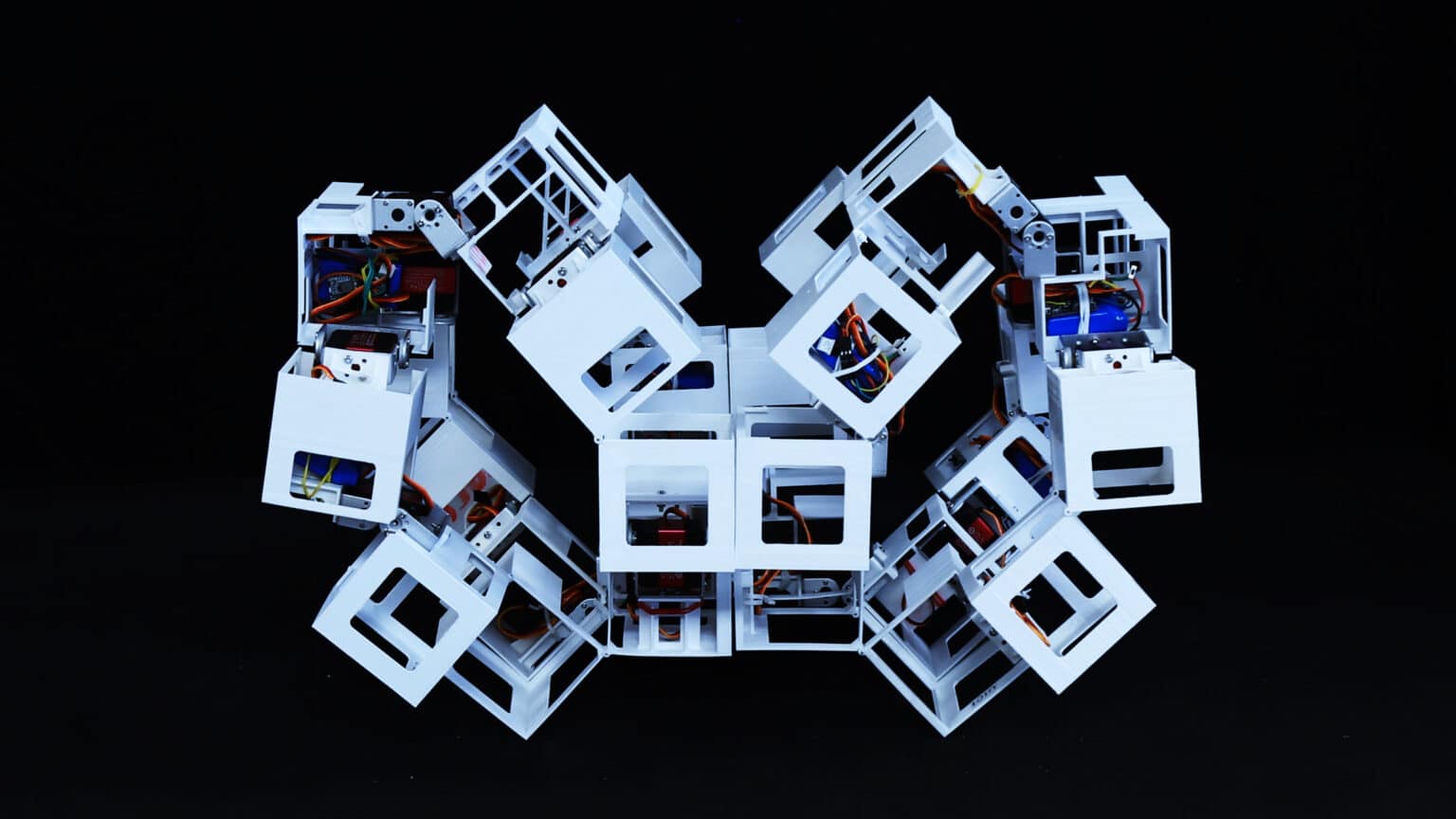
With only three active motors, a single cubed structure made of plastic can be transformed into over 1,000 configurations, according to NC State University research.
Using a 3D printer, engineers at NC State have found a way to assemble up to 36 hollow, plastic cubes into what they’ve dubbed “transformer bots.”
It might sound like something out of science fiction, but the bots weren’t inspired by characters like Optimus Prime and Bumblebee from the popular film and comic book series Transformers. Instead, the idea behind this real-life technology came from the paper-folding art of origami.
Rotating hinges — some fixed with metal pins, others activated wirelessly with a motor — allow the cubes to transform into so many different shapes.
“The question we’re asking is how to achieve a number of versatile shapes with the fewest number of actuators powering the shapeshifting,” says Jie Yin, associate professor of mechanical and aerospace engineering at NC State and a co-corresponding author of a paper describing the work. “Here we use a hierarchical concept observed in nature — like layered muscle fibers — but with plastic cubes to create a transforming robot.”
The untethered transformer bots Yin and his team created can move forward, backward and sideways merely by controlling how the shape of the structure changes. The bots can also transform relatively quickly from flat — or fully open — to a boxlike, fully closed larger cube.
The transformer bots also can carry loads of up to roughly three times their weight.
“We think these can be used as deployable, configurable space robots and habitats,” says Antonio Di Lallo, an NC State postdoctoral researcher and co-first author of the paper. “It’s modular, so you can send it to space flat and assemble it as a shelter or as a habitat, and then disassemble it.”
The findings were published earlier this year in Nature Communications.
In addition to Yin and Di Lallo, the paper, titled — “Adaptive hierarchical origami-based metastructures” — was co-authored by Hao Su, an associate professor of mechanical and aerospace engineering at NC State, and Yinding Chi, a former Ph.D. student at NC State. Junxi Zhu, an NC State Ph.D. student, was a co-corresponding author of the paper.
This article is based on a news release from NC State University.
- Categories: