Some Stirring Required: Fluid Mixing Enables Scalable Manufacturing of Soft Polymer Structures
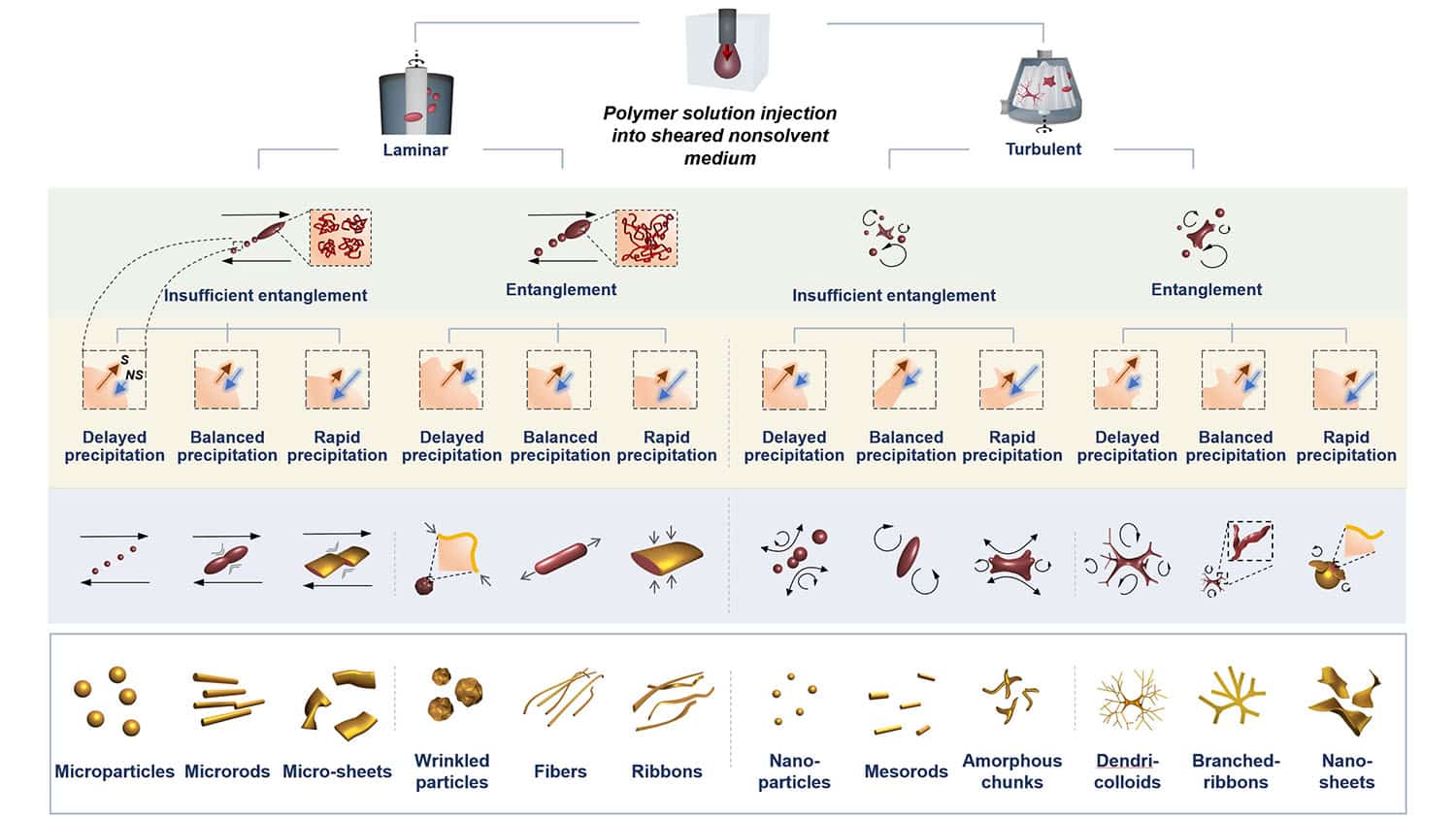
For Immediate Release
Researchers have developed and demonstrated an efficient and scalable technique that allows them to manufacture soft polymer materials in a dozen different structures, or “morphologies,” from ribbons and nanoscale sheets to rods and branched particles. The technique allows users to finely tune the morphology of the materials at the micro- and nano-scale.
“This advance is important because the technique can be used with a wide variety of polymers and biopolymers. Since the morphology of these polymeric micro- and nanostructures is critical for their applications, it allows us to obtain new polymer functionalities by simply controlling structure instead of polymer chemistry,” says Orlin Velev, corresponding author of the paper and the S. Frank and Doris Culberson Distinguished Professor of Chemical and Biomolecular Engineering at North Carolina State University. “For example, the nanosheets can be used in designing better batteries, whereas dendricolloids – branching networks of polymer fibers that have exceptionally high surface area – can be used in environmental remediation technologies or creation of novel lightweight metamaterials.”
Fundamentally, all of the different morphologies are produced using a well-known process called polymer precipitation. In this process, a polymer is dissolved into a solvent, producing a polymer solution. That polymer solution is then introduced into a second liquid, which makes the polymer come back together as soft matter.
What’s new here is that the researchers have discovered how to precisely control the structure of the resulting polymer soft matter by manipulating three sets of parameters during the manufacturing process.
The first set of parameters is the shear rate, which refers to how quickly the liquids are stirred when the two liquids are mixed together. The second set of parameters is the concentration of the polymer in the polymer solution. The last set of parameters is the composition of the solvent that the polymer was initially dissolved in, as well as the composition of the liquid that the polymer solution is added to.
“We identified the critical parameters that affect the final morphology of the polymeric materials, which in turn gives us a great deal of control and versatility” says Rachel Bang, first author of the paper and a recent Ph.D. graduate from NC State. “Because we now understand the role of each of these factors and how they all influence each other, we can reproducibly fine-tune the polymeric particle morphology.”
“Even though we have demonstrated how to produce a dozen different morphologies, we are still in the early stages of exploring all of the possible outcomes and applications,” Velev says.
The researchers have already demonstrated that the dendricolloids can be used to make membranes for growing live cells, or to create hydrophobic or hydrophilic coatings. The researchers have also worked with collaborators to demonstrate that the nanosheets have potential for use as more efficient separators in lithium-ion batteries.
“The technique can also be used with a variety of natural biopolymers, such as plant proteins, and it could be used to support a variety of applications, such as the development of plant-based meat analogues, which requires precise control of protein particle morphologies at multiple length scales,” adds co-author Prof. Simeon Stoyanov of the Singapore Institute of Technology and Wageningen University in the Netherlands. “In addition, because our technique is based on mixing liquids using conventional mixers, it can be easily scaled up for practical manufacturing.”
“We are currently working with food science researchers to determine how protein microrods could be used to control the texture of some food products,” Velev says. “And we are also working with collaborators to explore how our technique can be used to produce biopolymer-based materials for use in biodegradable soft electronics.
“We are open to working with additional collaborators to explore potential applications for the polymers and biopolymers across all of these morphologies.”
NC State has issued or pending patents on the shear fabrication of microrods, nanofibers, dendricolloids and their application in electrochemical energy sources.
The paper, “Fluid Flow Templating of Polymeric Soft Matter with Diverse Morphologies,” is published open access in the journal Advanced Materials. The paper is also co-authored by Sangchul Roh and Austin Williams, former Ph.D. students at NC State.
This work was accomplished with support from the National Science Foundation’s Nanomanufacturing Program, under grant CMMI-1825476. The work received additional support from NSF under grants EFMA-2029327 and CMMI-2134664.
-shipman-
Note to Editors: The study abstract follows.
“Fluid Flow Templating of Polymeric Soft Matter with Diverse Morphologies”
Authors: Rachel S. Bang, Sangchul Roh, Austin H. Williams and Orlin D. Velev, North Carolina State University; Simeon D. Stoyanov, Singapore Institute of Technology
Published: Feb. 25, Advanced Materials
DOI: 10.1002/adma.202211438
Abstract: It is challenging to find a conventional nanofabrication technique that can consistently produce soft polymeric matter of high surface area and nanoscale morphology in a way that is scalable, versatile, and easily tunable. Here, we explore the capabilities of a universal method for fabricating diverse nano- and microscale morphologies based on polymer precipitation templated by the fluid streamlines in multiphasic flow. We show that while the procedure is operationally simple, various combinations of its intertwined mechanisms can controllably and reproducibly lead to the formation of an extraordinary wide range of colloidal morphologies. By systematically investigating the process conditions, we identified twelve distinct classes of polymer micro- and nanostructures, including particles, rods, ribbons, nanosheets and soft dendritic colloids (dendricolloids). The outcomes are interpreted by delineating the physical processes into three stages: hydrodynamic shear, capillary and mechanical breakup, and polymer precipitation rate. The insights into the underlying fundamental mechanisms guide us towards developing a versatile and scalable nanofabrication platform. We verify that the liquid shear-based technique is versatile and works well with many chemically diverse polymers and biopolymers, showing potential as a universal tool for simple and scalable nanofabrication of many morphologically distinct soft matter classes.
- Categories: