Dielectric Film Has Refractive Index Close to Air for Photonics Applications
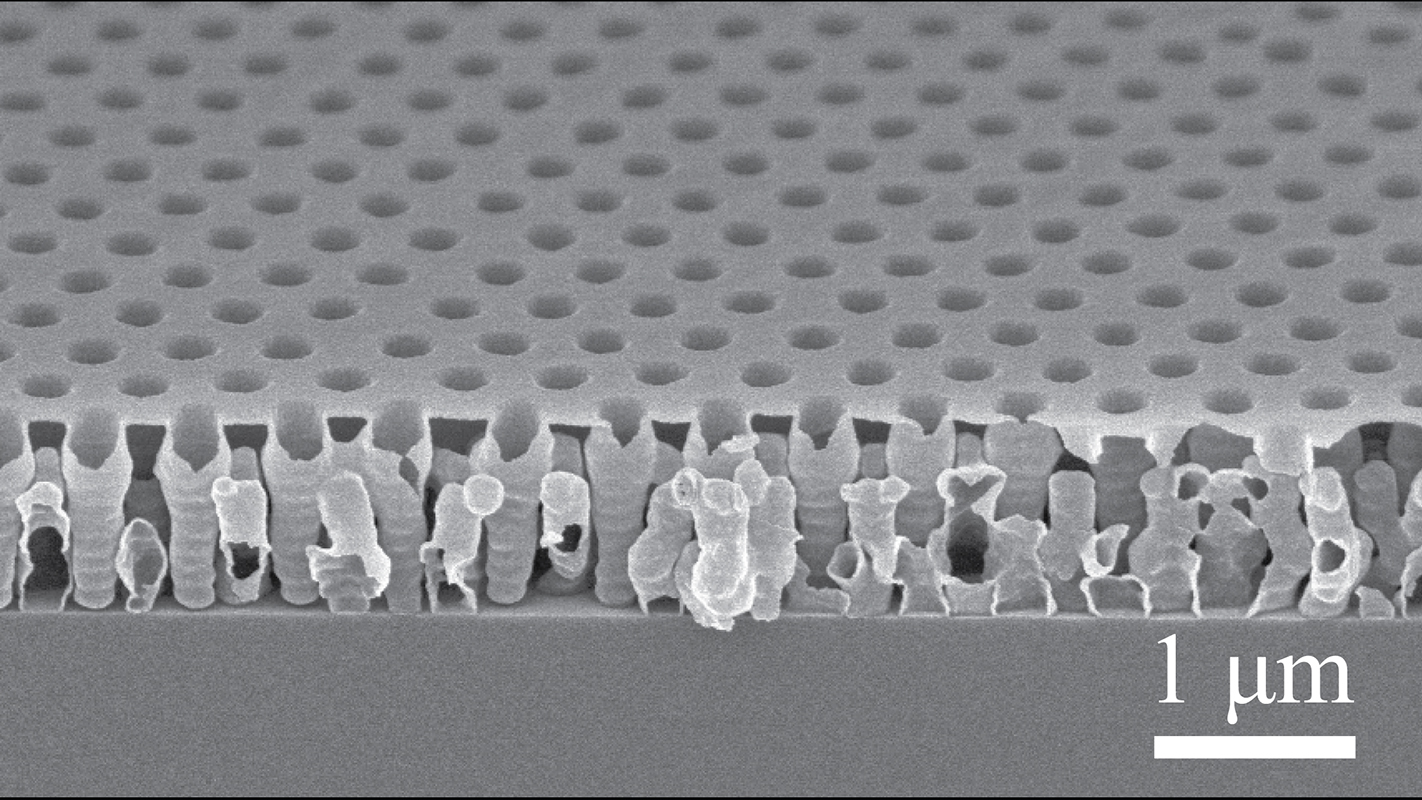
For Immediate Release
Researchers from North Carolina State University have developed a dielectric film that has optical and electrical properties similar to air, but is strong enough to be incorporated into electronic and photonic devices – making them both more efficient and more mechanically stable.
At issue is something called refractive index, which measures how much light bends when it moves through a substance. Air, for example, has a refractive index of 1, while water has a refractive index of 1.33 – which is why a straw appears to bend when you put it in a glass of water.
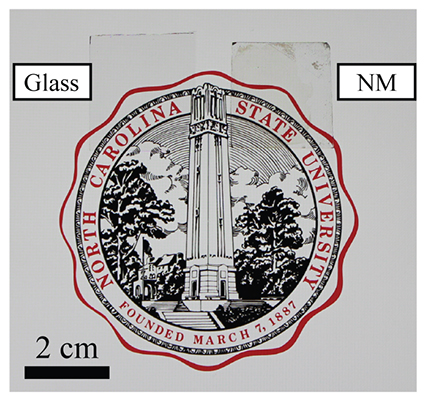
Photonic devices require a high contrast between its component materials, with some components having a high refractive index and others have a low one. The higher the contrast between those materials, the more efficient the photonic device is – and the better it performs. Air has the lowest refractive index, but it isn’t mechanically stable. And the lowest refractive index found in solid, naturally occurring materials is 1.39.
But now researchers have developed a film made of aluminum oxide that has a refractive index as low as 1.025 but that is mechanically stiff.
“By manipulating the structure of the aluminum oxide, which is dielectric, we’ve improved both its optical and mechanical properties,” says Chih-Hao Chang, corresponding author of a paper on the work and an assistant professor of mechanical and aerospace engineering at NC State. Dielectrics are insulator materials that are used in an enormous array of consumer products. For example, every handheld device has hundreds of capacitors, which are dielectric components that can store and manage electric charge.
“The key to the film’s performance is the highly-ordered spacing of the pores, which gives it a more mechanically robust structure without impairing the refractive index,” says Xu Zhang, lead author of the paper and a Ph.D. student at NC State.
The researchers make the film by first using a nanolithography technique developed in Chang’s lab to create highly-ordered pores in a polymer substrate. That porous polymer then serves as a template, which the researchers coats with a thin layer of aluminum oxide using atomic layer deposition. The polymer is then burned off, leaving behind a three-dimensional aluminum oxide coating.
“We are able to control the thickness of the aluminum oxide, creating a coating between two nanometers and 20 nanometers thick,” Zhang says. “Using zinc oxide in the same process, we can create a thicker coating. And the thickness of the coating controls and allows us to design the refractive index of the film.” Regardless of the how thick the coating is, the film itself is approximately one micrometer thick.
“The steps in the process are potentially scalable, and are compatible with existing chip manufacturing processes,” Chang says. “Our next steps include integrating these materials into functional optical and electronic devices.”
The paper, “Ordered Three-Dimensional Thin-Shell Nanolattice Materials with Near-Unity Refractive Indices,” is published online in the journal Advanced Functional Materials. The paper was co-authored by Abhijeet Bagal, Erinn Dandley, Junjie Zhao, Chrisopher Oldham and Gregory Parsons of NC State; and by Bae-Ian Wu of the Air Force Research Laboratory.
The work was done with support from the Air Force Research Laboratory and from NASA under grant NNX12AQ46G.
-shipman-
Note to Editors: The study abstract follows.
“Ordered Three-Dimensional Thin-Shell Nanolattice Materials with Near-Unity Refractive Indices”
Authors: Xu A. Zhang, Abhijeet Bagal, Erinn C. Dandley, Junjie Zhao, Chrisopher J. Oldham, Gregory N. Parsons and Chih-Hao Chang, North Carolina State University; Bae-Ian Wu, Air Force Research Laboratory
Published: Oct. 12, Advanced Functional Materials
DOI: 10.1002/adfm.201502854
Abstract: The refractive indices of naturally occurring materials are limited, and there exists an index gap between indices of air and available solid materials. With many photonics and electronics applications, there has been considerable effort in creating artificial materials with optical and dielectric properties similar to air while simultaneously being mechanically stable to bear load. Here we demonstrate a class of ordered nanolattice materials consisting of periodic thin-shell structures with near-unity refractive index and high stiffness. Using a combination of three-dimensional nanolithography and atomic layer deposition, these ordered nanostructured material have reduced optical scattering and improved mechanical stability compared to existing randomly porous materials. Using ZnO and Al2O3 as the building materials, refractive indices from 1.3 down to 1.025 were achieved. The experimental data can be accurately described by Maxwell-Garnett effective media theory, which can provide a guide for index design. The demonstrated low-index, low-scattering, and high-stiffness materials can serve as high-quality optical films in multilayer photonic structures, waveguides, resonators, and ultra-low-k dielectrics.
- Categories: