‘Digital Denim’ Is a Pretty Good Match for the Real Thing, Experts Say
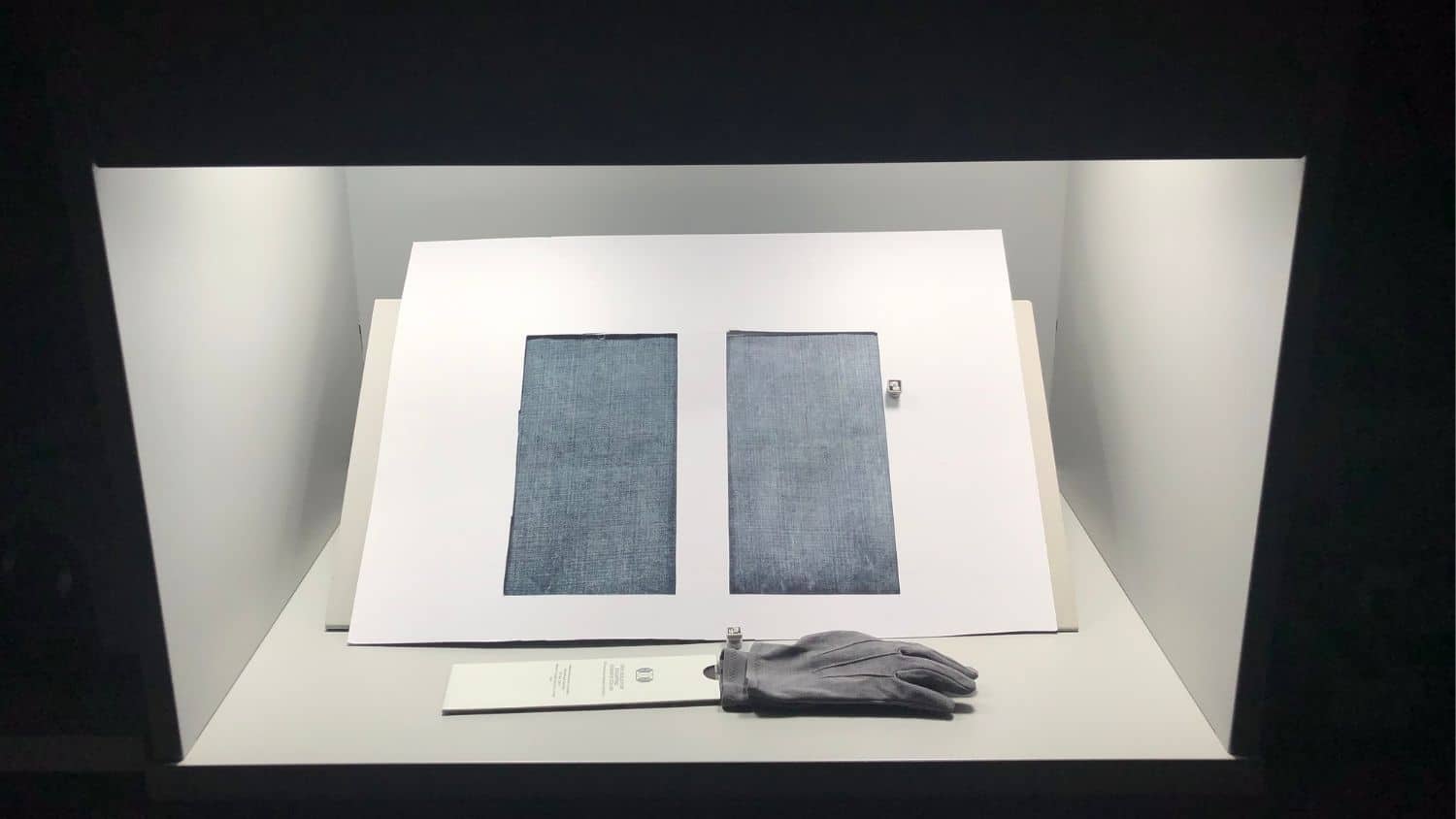
Drop by drop, researchers from North Carolina State University printed ink on cotton fabric to make “digital” denim fabric resembling six different styles of jeans. When they asked a team of textile experts, they found that overall, the samples made with the computer and printer were a good match on average for denim made using traditional, more labor-intensive methods.
However, in the Journal of Imaging, Science and Technology, the researchers reported that certain styles of jeans were easier to replicate using inkjet printing than others, and certain features, like color, were more easily replicated. With further study, researchers said they expect digital printing will be a viable method for making new jean products in the future, with less waste.
The Abstract spoke with study co-author Lisa Chapman, associate professor of textile and apparel technology and management at NC State, and lead author Ming Wang, a former graduate student at NC State, about the study.
The Abstract: Why were you interested in printing jeans digitally?
Chapman: Denim is a staple of our wardrobe. Almost everybody has several pairs of jeans in their closet. It’s a really popular item. It’s also one of those garments that’s sold worldwide. But the process for making denim is water-intensive. One of the things the industry is looking at is: How do you reduce the amount of water that’s used for denim?
Wang: To make jeans, the cotton yarn is dyed, and then there are finishing and washing processes that give jeans a certain look. Those processes can have a lot of negative environmental impacts such as water pollution and energy consumption. I wanted to explore another way to produce the same look of the denim that is more environmentally friendly.
TA: What is inkjet printing? Why is it used in textile manufacturing?
Chapman: Inkjet printing is really similar to your inkjet printer at home in that it’s going to jet droplets of ink onto the fabric. But in this case, it’s dropping textile colorant onto the surface of the fabric.
We consider it an emerging technology in that it’s still fairly small market share in textiles. But it has potential mainly because it uses less water, it uses less energy and it’s a print-on-demand process. So you’re eliminating some of the steps in the coloration process, and you have unlimited colors. To print using the traditional process, as you increase the number of colors, you increase the cost of the design. Inkjet printing is not like that; 200 colors is the same as two colors in cost.
At one point in the history of apparel, and in home furnishings, we had a lot of the same products. We would print lots of yards of the same design. Now we’ve moved to a consumer group that demands a lot of variety. When you have a lot of variety, you have more prints and you have smaller production runs and costs of the screen can be really expensive. Inkjet printing becomes more cost effective.
TA: In your experiment, how did you create the digital denim?
Wang: I used a high resolution scanner to scan a very high resolution image of the jean samples, then transferred it to a computer file that can contain the color and transparency information. Then I chose a pre-treated fabric that has the same weight and texture as the traditional jean samples. In the digital print lab, I had access to four different inkjet printers. After struggling to find the right ink and printer, I chose the latex printer, which is more environmentally friendly. I chose six different denim types that have different washing effects. We found digital printing can reproduce all of those effects.
TA: What did the expert panel say about the digital denim quality?
Wang: We found 12 experts from the textile industry who have a lot of experience, especially on denim and color matching. We asked them to compare the digital denim and the traditional jean samples. For color, the traditional and digital denim were very close. On a scale from one to five, with one as the greatest difference, five means there is no difference, the average score for color was around three or above three. Which means we had a good match for color.
Besides color, we also evaluated the line quality, the texture, the lightness, and overall match. What we found is that it’s very hard to achieve the line quality and texture. We think the reason might be that the traditional dyeing has high ink penetration. But for digital printing, it’s printing on the surface of the fabric, and it’s not penetrating that much into the fabric. That could cause the difference in line quality and texture.
TA: What is the future of digital denim?
Wang: If someone could solve the ink penetration problem, I think we could mass produce denim products with a high speed printer. It could bring the cost of production down. However, since mass production is not quite realistic yet, we could use digital printing for high-end denim products like for home textiles or apparel. For kids, they are growing every day, so you could have something that looks like jeans.
Chapman: It may be difficult to replace traditional denim, but there are other markets where this could do a much better job. Jeggings is a great example. In addition to infant wear, there are situations where you want the denim look, but you want a higher drape and a softer fabric, like dress shirts or women’s dresses.
TA: What is the future of digital printing for textiles?
Chapman: While there is a pretty high learning curve for digital printing, there are also advantages with reduced energy use, chemicals, and water waste when we’re comparing digital printing to screen printing. The dot-com market is also going to drive digital printing. We’ll be looking at new technologies that speed up the production cycle to get goods to consumers faster.
- Categories: